
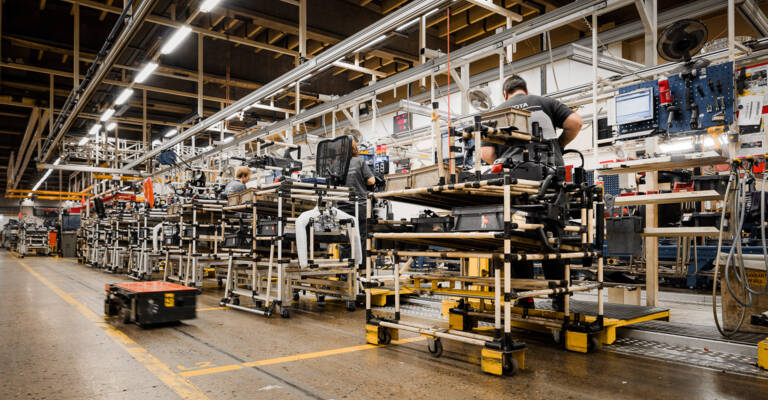
Taking a trip to the factory floor to converse with workers reveals opportunities for improvements.

Standardize workplace tasks to give employees a reliable job method.This will help create quality product the first time around. Build a positive company culture that assists the company with fixing problems as soon as they occur.Level the workload to prevent burnout, this is referred to as heijunka or “work like a tortoise, not the hare.”.This is the basic idea of Just-in-Time production as it reduces inventory and enables the company to satisfy the customer’s demands. Avoid overproduction with pull systems.This in turn will help to bring production problems into view. Implement a long-term philosophy even if it sacrifices short-term financial goals of the company.Each of the following fourteen principles are integral to the success of the Toyota Production System: To understand TPS, it is important to learn about the principles used in this system. No matter the type of facility being run, learning about TPS can help inspire innovation and prepare a company to implement a variety of workplace improvements. TPS is recognized as one of the major contributors to the development of Lean manufacturing and many other Lean concepts that people are familiar with today. Today, Toyota is recognized as a leader in the auto manufacturing industry, and most other manufacturers use the Toyota Production System at least in some fashion.
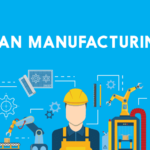
Japanese industrial engineers Taiichi Ohno and Eiji Toyoda are the two primary individuals credited with the development of this system. Applying the Toyota Production System into any business model makes for “living” in that metaphorical house better for those within the organization. TPS is made to achieve the same goals regarding updating old and worn-out systems for ones that are new and improved. A well-made home often still has to undergo renovations as time passes whether that be because of outdated materials or broken appliances. Whenever learning about TPS, it’s common to visually depict the system as a house. The system helps bring improved organization efforts to a facility, reduces waste, and can improve the bottom line of companies that choose to adopt it. However, it has been modified to work with other manufacturing outlets and businesses as well. Developed by the Japanese auto manufacturing company Toyota, this Lean method has a special focus on auto manufacturing. The Toyota Production System, also referred to as TPS, is a strategy that helps organize the manufacturing and logistical aspects of a business. History of the Toyota Production System.
